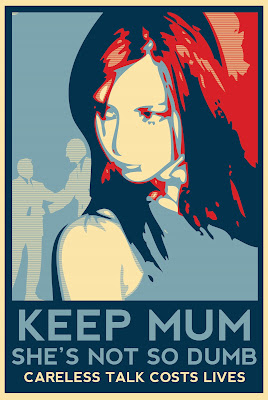
For our final project, we were assigned the open job to create a modern 'propaganda' poster using a theme from propaganda from 1900-1950. I did some research, looked into russian propaganda, but I decided to go with the recognizable british propaganda theme from WWII, "Keep mum, she's not so dumb!"
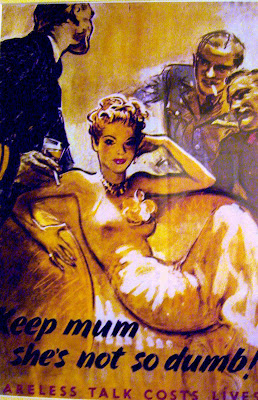
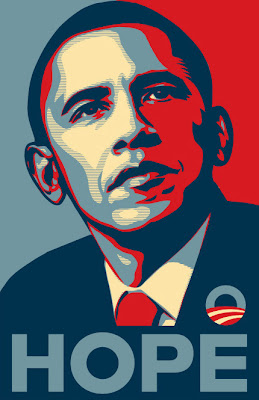
I decided, even though it might come off as overdone, to replicate the Obama hope poster from the 2008 campaign. I didn't want to use a stock image of some girl, so I actually went online to a fast-moving message board I frequent, and asked for a girl to quickly post a shot of her facing forward and looking somewhat sultry. I got many responses, but I decided upon this shot:
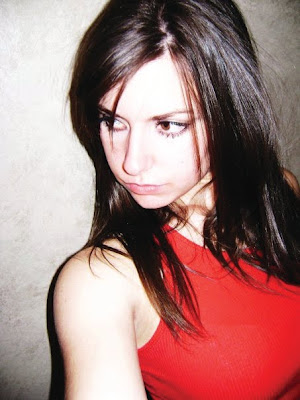
Then my job was to replicate the style of the original poster as closely as possible. I found an offshoot of the original font, spent hours in illustrator with colors and filters, and finally came out with the finished product seen above! I do not think I replicated the obama poster well enough, but I do like how the poster turned out in the final printed product.